Reviewed and Approved by Matilda Baghdasarian, MBA, Associate Director/Safety Officer, Certified Laboratories
1-Minute Summary
- Photostability testing simulates long-term light exposure to ensure OTC drug products and cosmetics remain safe and effective throughout their shelf life.
- The FDA recommends photostability testing as part of stress testing, referencing ICH Q1B as the standard guideline.
- Products with light-sensitive ingredients or clear packaging are especially vulnerable and should be tested under ICH Q1B Option 2.
- Photostability results guide critical decisions about packaging, labeling, and storage, helping manufacturers avoid costly reformulations and maintain brand integrity.
A Cautionary Tale in Photostability
Imagine that you’ve developed a promising new translucent shampoo packaged in a beautiful clear bottle. The formulation looks great, performs well, and early feedback is positive.
But within weeks of distribution, complaints begin trickling in due to discoloration and foul odor.
The culprit? Light degradation. The product, packaged in clear plastic for visual appeal, wasn’t tested for photostability. Exposure to ambient light, such as during shipping, on store shelves, and even in the shower, caused the active ingredient to break down, leading to quality failures and brand risk.
This scenario is exactly why photostability testing is a critical part of quality control for cosmetics and OTC drug products.
In this article, we’ll explore:
- What photostability testing is and why it matters.
- Which OTC products require testing.
- How testing is performed under ICH Q1B guidelines.
- What to expect from the process.
What Is Photostability Testing?
Photostability refers to how well a product resists chemical changes when exposed to light.
Over time, certain ingredients can degrade in response to UV or visible light, which may alter their chemical structure, potency, appearance, or even safety.
Photostability testing is designed to simulate long-term light exposure and determine if a product remains stable or requires special protection. It’s a vital part of the stability profile and, by extension, the quality assurance process.
It’s a key part of your overall stability testing program for your OTC, cosmetic, and other products.
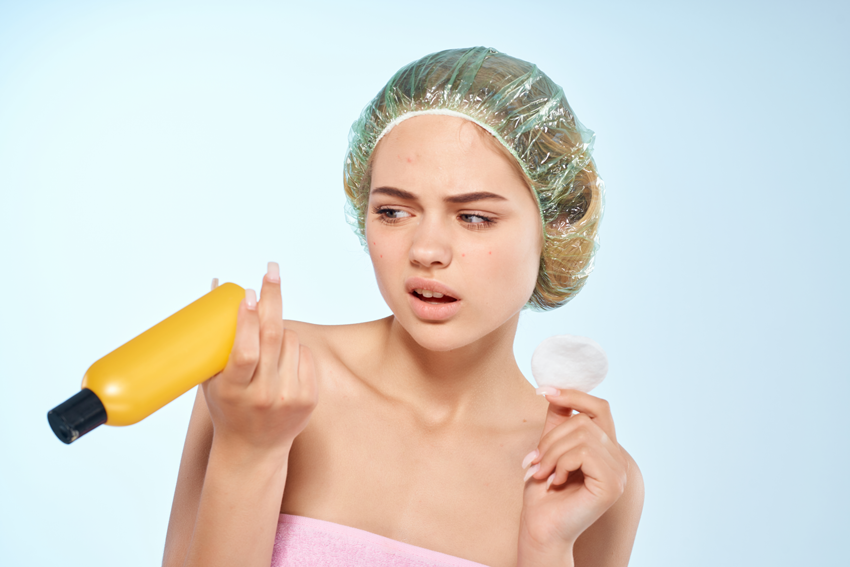
What Products Require Photostability Testing?
Not every cosmetic or OTC drug product is vulnerable to light degradation, but many are. Products commonly tested include…
- Those containing light-sensitive APIs (e.g., retinoids, vitamin C, nitroglycerin).
- Solutions, gels, creams, and sprays.
- Products in clear or translucent packaging.
Example: A shampoo may look clear and stable at first, but after light exposure, it could oxidize and turn yellow, which is not apparent without testing.
Photostability testing helps uncover these vulnerabilities early, before the product reaches consumers.
Understanding ICH Q1B: The Regulatory Foundation
Photostability testing is guided globally by ICH Q1B, which outlines standardized methods to evaluate a product’s light stability.
While the U.S. Food and Drug Administration (FDA) does not mandate photostability testing for all OTC products, it strongly recommends it for products at risk of light degradation. The agency’s position is clear in its Guidance for Industry Q1A(R2) Stability Testing of New Drug Substances and Products:
“Photostability testing should be an integral part of stress testing. The standard conditions for photostability testing are described in ICH Q1B Photostability Testing of New Drug Substances and Products.”
This guidance contains non-binding recommendations, but it provides essential insight into the FDA’s current thinking and expectations for drug product stability. Especially for OTC manufacturers submitting NDAs or ANDAs, or simply wanting to produce stable, compliant products, following ICH Q1B is a best practice.
How Photostability Testing Is Performed
At Certified Laboratories, we use ICH Q1B Option 2, a highly reproducible method involving…
- 200 W/m² irradiance (broad spectrum from 300 to 800 nm).
- 1.2 million lux-hours of light exposure.
- Simulated 6 months of ambient indoor light exposure or 10 days under a lightbox.
There are two testing approaches.
- Artificial Light Exposure: Fluorescent and UV light sources mimic sunlight and indoor lighting.
- Solar Simulation: High-intensity sunlight simulators can be used for advanced studies.
Products are tested in both primary packaging (e.g., bottle or tube) and secondary packaging (e.g., carton). Conditions such as temperature and humidity are carefully controlled to ensure accurate results.
How Long Does Photostability Testing Take?
Once your test protocol is approved, photostability testing typically takes 7–10 business days to complete.
Steps include…
- Protocol Development: Define test method, exposure duration, and evaluation criteria.
- Sample Preparation: Product is packaged as intended for market and placed in the chamber.
- Chamber Calibration: Light intensity and spectrum are validated for regulatory compliance.
Certified Laboratories manages this process from start to finish, helping you meet tight timelines.
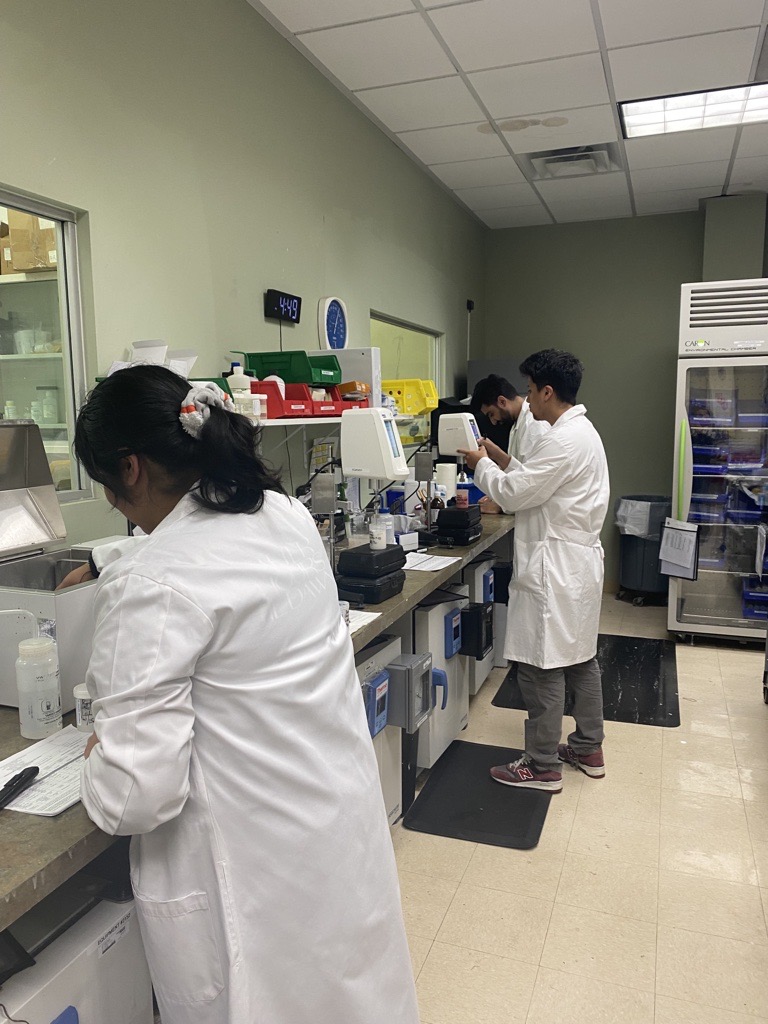
What Do Photostability Results Tell You?
Photostability testing can reveal how a product will perform under real-world lighting conditions over time. Results typically fall into two categories:
- Stable Under Light: No significant changes in potency, appearance, or chemical profile. Standard packaging and labeling may be sufficient.
- Light-Induced Degradation Observed: Changes in color, strength, or impurities suggest the need for protective packaging (e.g., amber bottles, foil pouches) and label updates (“Store in a dark place”).
These outcomes inform shelf life, packaging design, and consumer handling instructions.
Revisited Case Study – A Light-Sensitive Shampoo
Let’s revisit our shampoo example.
Photostability testing was skipped to save time. The product launched in clear plastic bottles, which are eye-catching, but unprotected. Within days of light exposure, the product oxidized, became discolored, and produced a foul odor, clearly not good for the brand.
Had the manufacturer followed ICH Q1B guidelines, this risk would’ve been identified. The team could have…
- Reformulated or adjusted ingredient levels.
- Selected amber or UV-blocking packaging.
- Added “protect from light” labeling.
Instead, they faced product returns, quality complaints, and brand damage. A costly mistake that photostability testing could have prevented.
Why Companies Do Stability Testing—and Why They Trust Certified Laboratories
As we’ve seen, companies invest in stability testing because they need to be confident that their products will maintain quality, safety, and effectiveness over time. Whether it’s sitting in a warehouse, traveling cross-country, or stored in a consumer’s bathroom cabinet, an OTC drug or cosmetic must perform exactly as intended.
Photostability testing, in particular, helps companies…
- Confirm that light exposure won’t cause degradation or loss of potency.
- Establish accurate expiration dates, period-after-opening guidelines, and best-by dates.
- Develop proper storage instructions to protect product integrity.
- Strengthen their brand reputation by ensuring consistent customer experiences.
At Certified Laboratories, we’re proud to be a trusted partner for photostability and overall stability testing. Companies choose us because we…
- Operate over 100 calibrated stability chambers across our national lab network.
- Follow ICH guidelines, including ICH Q1B Option 2 for photostability.
- Work with you to design stability protocols that match your product needs, budget, and timelines.
- Deliver clear, actionable reports that make decision-making easy. In fact, many of our clients tell us they appreciate how easy our reports are to interpret and use internally.
- Offer technical expertise at your fingertips — you can talk directly with our scientists if you have questions or need guidance.
- Can support a wide variety of products, including OTC drugs, cosmetics, and dietary supplements.
You might think, “Why not perform stability testing in our in-house lab?” Using a third-party lab like Certified Laboratories provides advantages over in-house testing:
- Cost savings — Building and maintaining a compliant stability lab is expensive.
- Credibility — Third-party data is viewed as more objective and reliable by customers, auditors, and regulators.
- Expertise — Stability testing is complex. Our team has decades of experience designing and interpreting photostability studies across a broad range of industries.
Whether you’re launching a new product, troubleshooting stability concerns, or preparing for regulatory submissions, Certified Laboratories is ready to help you protect your product, your customers, and your brand.
Contact us today to get started with photostability testing you can trust.